China dominates the world’s production and processing of graphite, which is the largest component by weight in electric vehicle (EV) batteries, and one of the most pure forms of carbon. Minerals.net describes it as follows: “Graphite is a mineral composed exclusively of the element carbon. Graphite has the same chemical composition as diamond, which is also pure carbon, but the molecular structure of graphite and diamond is entirely different.”
Due to increasing EV sales, automakers are trying to lock in graphite supply from outside of China, as demand for EV batteries outpaces other uses for the mineral. In the past, automakers focused mainly on supplies of lithium and cobalt, but now they are looking for new producers, such as Madagascar and Mozambique, as this year electric vehicles are expected to account for over 50 percent of the natural graphite market. Each electric vehicle on average needs 50 to 100 kilograms of graphite in its battery pack for anodes, the negative electrodes of a battery, about twice the amount of lithium. The main use of graphite is in the steel industry and it is also used in brake linings, but EV sales are expected to more than triple by 2030 to 35 million from 2022, increasing graphite’s demand.
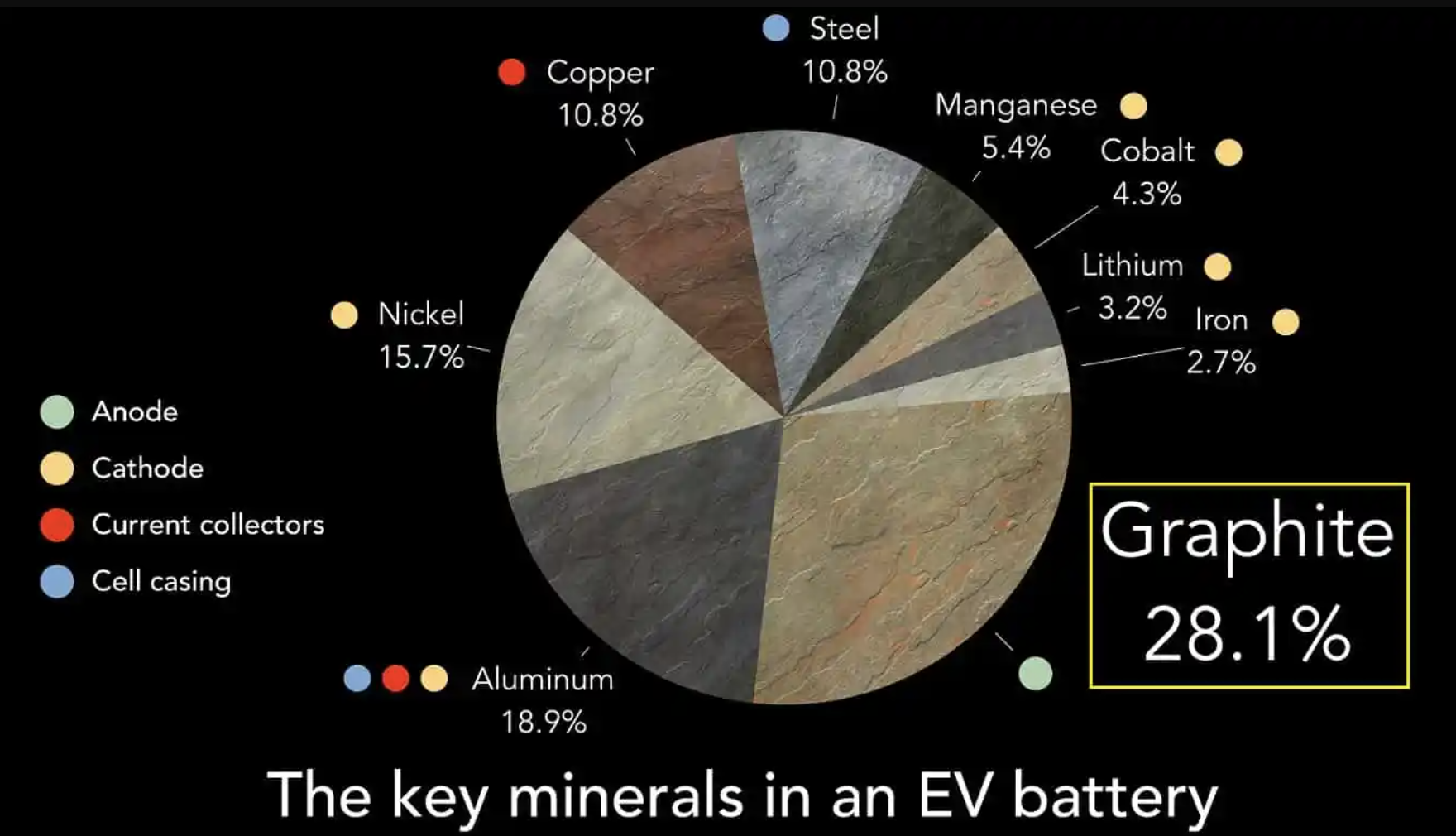
Shortages of graphite are expected in coming years, with a global supply deficit of 777,000 metric tons by 2030. According to Benchmark Mineral Intelligence, about $12 billion of investment is needed by 2030 in graphite and 97 new mines are required by 2035 to meet demand. China produces 61 percent of global natural graphite and 98 percent of the final processed material to make battery anodes and it is expected to maintain its dominance. By 2032, China is expected to control 79 percent of production of a type of processed graphite – uncoated spheroidised purified graphite – compared to 100 percent in 2022.
Chinese market dominance makes it difficult for automakers who want to qualify for EV subsidies under the U.S. Inflation Reduction Act (IRA), which requires certain high percentages of battery components to be produced in the United States, or in a country with which it has a free trade agreement. The European Union proposed legislation to reduce dependency on any one country for any key raw material to 65 percent by 2030. This compares to 30 percent of the world’s oil supply provided by the 13 nations of OPEC.
Western auto groups are focusing on deals with graphite mines partly because it is around 55 percent less carbon intensive to produce anodes with natural material compared to synthetic graphite made from petroleum products such as petroleum coke. Currently, synthetic graphite anodes dominate in terms of market share, accounting for approximately 57 percent of the anode market. Synthetic graphite anode supply grew by more than 30 percent during 2022, and is expected to surpass that in 2023, given that a supply deficit may be developing for natural graphite feedstock.
Natural graphite anodes tend to be cheaper and are beneficial for cell capacity and power output, allowing cars to run further distances before charging. Another anode ingredient is silicon, which also enables an EV to drive longer distances before recharging. Currently, the maximum amount of silicon added to batteries is about 10 percent because the material expands during use and can degrade the battery. Companies are working on technology that would allow larger amounts of silicon, which could encroach on graphite’s demand.
Conclusion
Graphite may be the next mineral of concern to automakers as it is the largest component of EV batteries by weight. Currently, the steel industry is the major user of graphite, but because EV sales are expected to increase significantly, graphite is expected to be the next mineral to face large price increases. As such, automakers are looking for graphite supplies in countries other than China, who dominates the world in both the production and the processing of graphite. The current alternative is synthetic graphite made from petroleum coke, but it is much more carbon intensive than natural graphite.